In the dynamic chronicle of sustainable industrial practices, the continuation of innovative solutions to address the formidable challenges of water treatment and separation processes has become predominant. The human population worldwide is sharply increasing, leading to the daily production of tons of wastewater in the domestic, industrial, and agricultural regions, and obviously representing an essential part of the value chain in all life sectors [1].
Fossil Fuel has been one of the most conducive sources of energy for more than a century. In oilfields and refineries, water is considered the largest waste stream, and it has a high number of hydrocarbons, heavy metals, and other pollutants [2]. This produced water (PW) may account for 80% of the waste and residuals generated from natural gas production operations [3]. It is estimated that the petroleum industry generates about 250 million barrels (39.75 million m3) per day of PW, representing a significant and major volume of a waste stream byproduct with a water cut of 70%. It is significant to state that the oilfield-produced water is toxic, saline, and copious. When disposed of without appropriate treatment, it will cause harm to both the environment and human health [4]. This water has two main origins: first, the water originally in place inside and around the reservoir, and second, the water injected into the reservoir during production activities [5].
Produced water consists of distinct significant components: oil and grease, suspended solids, dissolved solids, heavy metals, radioactive materials, bacteria, dissolved gases, and various other chemicals; these substances will impact the selection of treatment technologies [6]. The pollution of this PW is mainly associated with the interaction between the original composition of the water and the surrounding reservoir from one side and the added chemicals used throughout the life of the well [7]. Therefore, executing raw produced water into the environment can lead to important environmental effects, impacting human wellness and marine life.
Various expenditures have been made over the years to present distinct wastewater treatment technologies and to develop existing ones. This development faces the challenge of the complexity of the produced water. Given the wide variation in contaminants and concentrations in produced water, no single technology is universally optimal [8]. Traditional methods, such as gravity segregation, are inefficient and fail to meet current environmental standards. Other technologies include conventional filtration, coagulation-flocculation, biological treatment systems, chemical oxidation and many more. These treatments can be more efficient when applied in chemical dosages and external electric fields. However, these methods result in highly energy-intensive processes that ultimately cause more environmental harm than good. As such, membrane technology is now a widely used process in water and wastewater treatment due to its small size of equipment, less energy consumption and low capital cost.
Moreover, it has been regularly improved to satisfy many other important criteria such as efficiency, quality of permeate, and other technical necessities like membrane fouling. It is worth mentioning that the integration of other forms of technology, such as adsorption or even using two or more membrane processes, is regularly being explored, established, and even applied in various wastewater treatment facilities [9]. Moreover, Microfiltration (MF), Ultra-filtration (UF), Reverse Osmosis (RO), and Nanofiltration (NF) are various membrane types that can be integrated into the process to achieve treatment and environmental goals.
Besides, the literature mainly addresses the general implementation of these techniques for produced water treatment, frequently overlooking specific and real applications for the reuse of the treated water. This review embarks through the water-related challenges faced by the petroleum industry from production to treatment, considering the need for efficient treatment and management. Then, it focuses on real applications of different types of membranes used in the industry, as well as their structures and performance. The study continues to identify the prospective of membrane-based technologies and ends with important achievements in the purification of produced water coming from the oil fields. This review uses a comparative approach, examining current literature on membrane technologies in the oil and gas industry and highlighting the existing gaps.
In the petroleum industry, managing water production presents significant challenges both during and after the production phase. During production, water production is often inevitable, prompting the production team to minimise water volume to optimise hydrocarbon output and reduce the need for separation and treatment. Despite these efforts, substantial water volumes are continually produced throughout the lifetime of a well, and environmental regulations are becoming increasingly stringent. Consequently, effective treatment of produced water is necessary for proper management. This management involves either disposing of the water in the environment or reusing it in the petroleum and other industries. In general, the level of treatment required increases from disposal to industrial reuse, impacting the required purity of the treated water, the treatment process, and the technologies used. The following sections address the problems encountered with produced water during the production phase and the socio-economic challenges associated with its management and treatment.
Oil and gas reservoirs are commonly associated with water aquifers that negatively affect the hydrocarbon production rates and their recoveries. The impact of such aquifers depends on their activity levels, which vary in different reservoirs. For instance, a sharp increase in water cut is observed in aquifers of active water drive that leads the water to encroach on the hydrocarbon-bearing zones being produced. Consequently, this effect results in significant amounts of unrecovered hydrocarbons with a large production of contaminated water [10]. On the other hand, reservoir heterogeneity and low permeability can form barriers to water invasion in the producing zones. Naderi et al. [11] found that cumulative water production declines as heterogeneity of the reservoir increases when the reservoir is inclined at an angle below 14.4°.
Several phenomena are responsible for water production issues, including coning, cresting, fracturing, and fingering and channelling, as illustrated in Figure 1.
Phenomena increasing water production: coning (a), cresting (b), fractures (c), fingering (d)
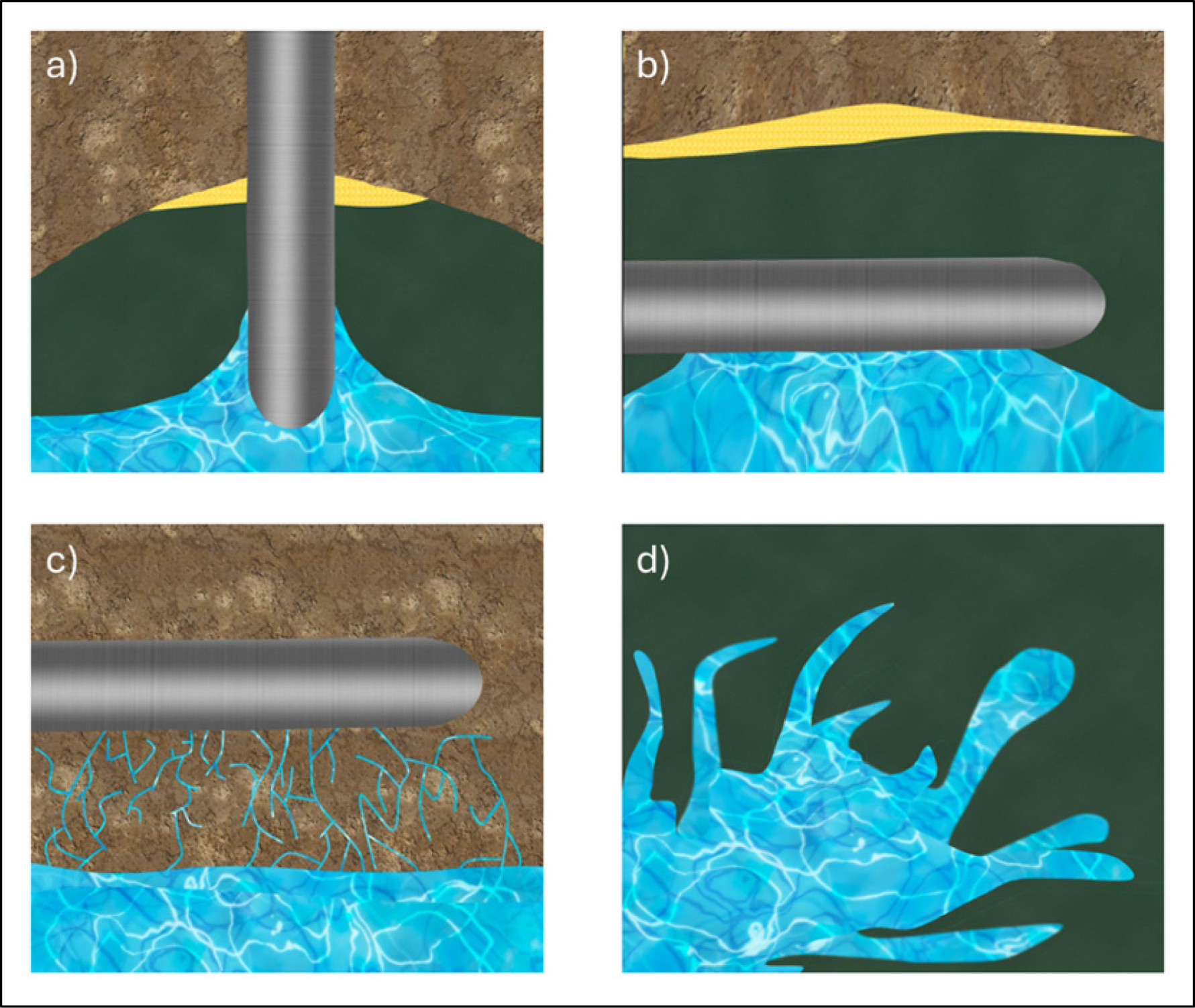
It describes the upward movement of water leading to alterations in the profiles of the oil-water contact (OWC) or gas-water contact (GWC) and causes an early breakthrough, which could entail a high water cut. Two main forces affect this phenomenon: the gravity force and the dynamic flow force. Coning generally occurs when the drawdown pressure exceeds the gravitational forces. In general, it is affected by the reservoir characteristics in terms of fluid and rock properties, as well as the reservoir geometry. It is important to note that it is mainly observed in vertical or slightly deviated wells, and its severity increases with higher vertical permeability.
Cresting is like water coning, but it mainly occurs in horizontal wells. With increased pressure drawdown, the viscous forces will overtake the impact of gravity and density aggregation present in the reservoir [12]. This situation will result in the upward movement of water above the hydrocarbon phases, leading to an early breakthrough. As previously mentioned in coning, this phenomenon is also affected by the reservoir rock and fluid properties and the reservoir geometry. The intensity of cresting depends on the aquifer size and the production rate.
Fluids tend to follow the path associated with the least resistance [13]. In rock formations, fluids are more likely to pass through fractures or micro-fractures, which offer the least resistance path compared to those connected by pores. Based on that, some reservoirs can be directly connected to aquifers through deep fractures. It motivates water to penetrate hydrocarbon-bearing zones and to increase water cuts during production [14]. In this context, He et al. [15] noticed that, despite the enhanced hydrocarbon production concept, hydraulic fracturing could be a good reason for an early water breakthrough.
Due to heterogeneity in reservoirs, high permeability zones are often embedded with low permeability layers. Water advances rapidly in these highly permeable zones, showing early water breakthroughs and high water cuts. It is known that water is generally injected into the formations to enhance the oil recovery by extracting the remaining hydrocarbons. In this case, the sweeping front will end up becoming unstable and causing fingering. In turn, slim and long fingers clearly prevent hydrocarbon recovery and keep a large area in the reservoir unswept [16].
Produced water management is dependent on several factors which will dictate its fate. It is highlighted in the regulatory obligations, the environmental impacts, the risks associated with the water, and the feasibility studies regarding the technical and economic aspects of the project and its alternatives [17]. Moreover, efficient management starts by decreasing the produced water volume through production considerations, such as minimising the volumes of injected water, optimising the selection of layers for production, and implementing downhole phase separations. Nonetheless, water will still be produced, and these quantities are usually managed as listed below from the most common practices to the least common ones [18]:
Injection in underground formations for disposal,
Usage in oil and gas activities, such as water injection,
Usage in industrial and agricultural processes after adequate treatment is implemented,
Disposal into the environment based on environmental regulations.
Managing produced water requires understanding the complexities of handling water generated during oil and gas extraction. In this aspect, it is critical to interpret its composition, mainly the organic and inorganic materials. This composition is not set constant everywhere in the world but differs greatly based on the formation geology, the location geography, and the hydrocarbon extraction process [19]. As mentioned previously, produced water can include oil and grease, total dissolved solids (TDS), total suspended solids (TSS), heavy metals, production additives, dissolved gases, BTEX (benzene, toluene, ethylbenzene, and xylenes), and naturally occurring radioactive materials [20]. TDS and chloride contents, which are representative of the salinity content of the produced water, pose a great obstacle to the reuse of produced water outside the oil and gas industry. A high salinity content makes the produced water unsuitable for industrial and agricultural processes.
Based on that, produced water treatment is required even for underground disposal purposes or injection activities to enhance hydrocarbon production [21]. It is especially necessary for volumes with high salinity, solids, and other contaminants presented in Table 1.
Produced water composition
Component | Concentration range [mg/L] | Reference | |
---|---|---|---|
Oil and grease Total dissolved solids (TDS) Total suspended solids (TSS) |
2–565 4000–50000 1.2–10,623 |
[22] [23] [22] |
|
Metals | |||
Barium | 0.058–850 | ||
Strontium | 500.01–6250 | ||
Cadmium | 0.0105–26.2 | ||
Chromium | 0.1963–97.2 | ||
Copper | 0.0613–89 | ||
Lead | 0.1340–205.8 | ||
Nickel | 0.0977–162 | ||
Zinc | 0.255–113.4 | ||
Iron | 0.7133–550.05 | [24] | |
Manganese | 0.0713–87.502 | ||
Arsenic | 0.1525–5.2387 | ||
Boron | 1.8873–50 | ||
Tin | 0.68 | ||
Aluminum | 205.2–360 | ||
Lithium | 26.5–32.019 | ||
Titanium | 0.36 | ||
Mercury | 0.0015 | ||
Dissolved oxygen | 8.2 | [22] | |
BTEX (benzene, toluene, ethylbenzene & xylenes | 0.73–24.1 | [20] | |
Naturally Occurring radio-active Materials (NORM) | |||
226Ra [Bq/L] | 0.3–16 | ||
228Ra [Bq/L] | 1.3–21 | [20] |
In general, produced water necessitates primary and secondary treatments. The primary treatment aims to remove large droplets of oil and grease, coarse solid particles, and gas bubbles, and it helps to amass charged particles, making the resulting effluent suitable for underground disposal [25]. Moreover, this treatment may be used to eliminate harmful bacteria and decompose additives that were mixed with the produced water [26]. The secondary treatment focuses on the removal of small droplets and dispersed solids using typical equipment such as gas flotation and hydro-cyclone units [27]. Then, treated water becomes suitable for injection operations in oil and gas activities and for discharge into the environment [28].
With freshwater becoming scarcer because of climate change, the need for reusing water in other industries becomes essential [29]. Here comes the role of the tertiary treatment, which is essential to remove the ultra-small particles and dispersed hydrocarbons to below 10 mg/L. A wide range of equipment can be used to ensure better results, such as nutshell or walnut shell filters, adsorption by activated carbon, biological treatments, and different types of membrane technologies, assuring the final treated water is adequate for utilisation in other proper industries [30].
The selection of the treatment level and technical units for produced water depends on several factors. First, the composition of the produced water, including contaminants like salts, heavy metals, and organic materials, is critical in determining the appropriate treatment technology. The end goal of water treatment is also essential; water for re-utilisation in other industries requires higher purity levels than water treated for disposal or reinjection. Additionally, the costs of installation, operation, and maintenance impact the economic feasibility of the treatment facilities. Energy requirements of the treatment processes also play a role; less energy-intensive processes are more cost-effective. Lastly, safety considerations are crucial, with process units needing to meet safety standards and risk management assessments [31].
Produced water reutilisation challenges
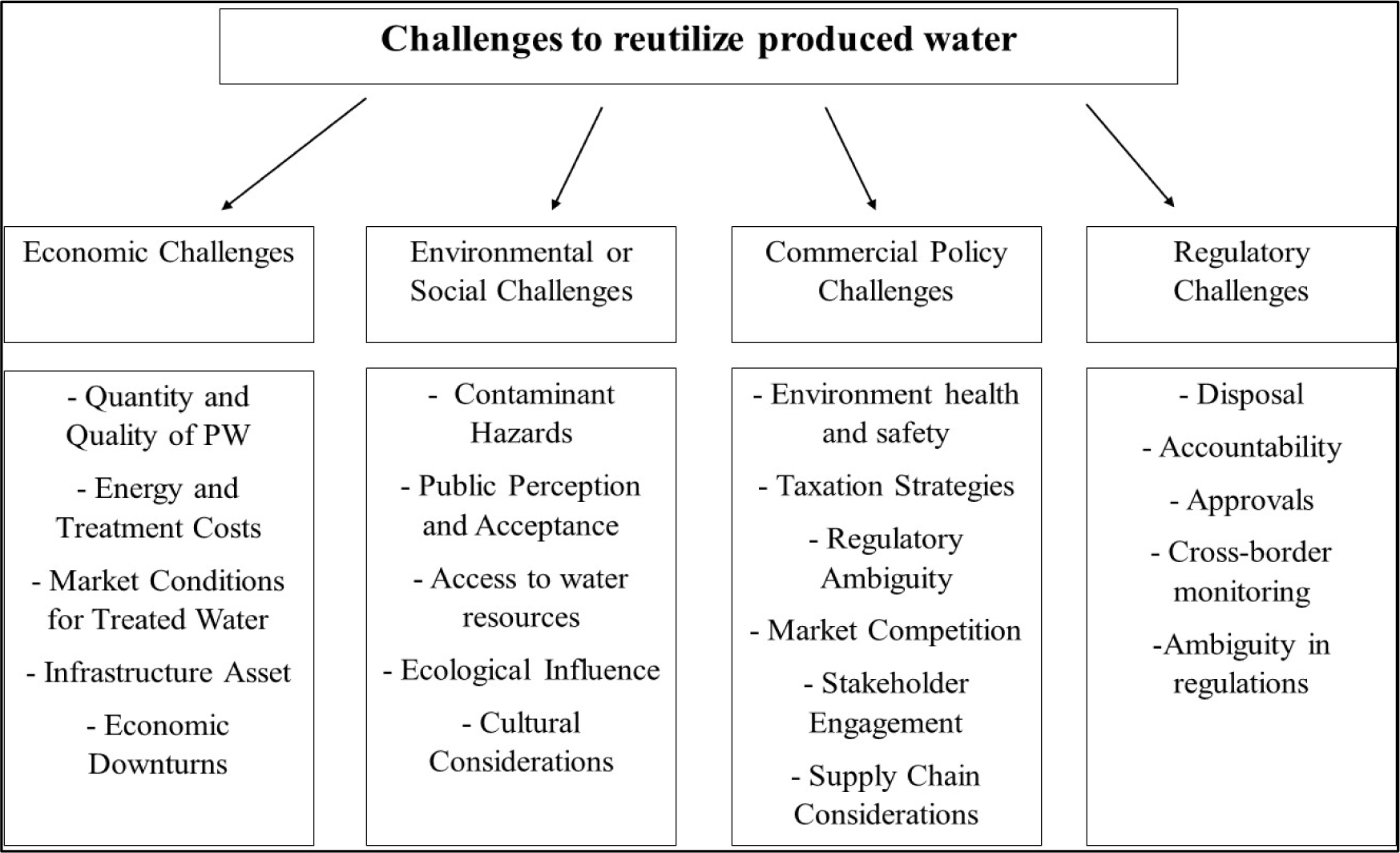
Despite the advantages of using treated produced water in many industries, this operation is faced with several challenges in different aspects, as shown in Figure 2. On the regulatory level, these challenges are represented by water quality requirements based on their end-use, permits and authorisations needed by governing bodies, and water ownership disputes [32]. The latter depends on the regulations in each country or state, where the water might not belong to the operators but to the government or landowners. For example, the Oslo and Paris Convention (OSPAR) stipulates a maximum allowed concentration of 30 mg/L of dispersed oil in water for monthly discharge into sea environments [33]. In contrast, the Environmental Protection Agency (EPA) in the United States sets discharge conditions based on the production site's location − whether offshore, onshore, coastal, or agricultural. This location-specific classification means that contaminant concentration regulations vary by region, with different acceptable discharge conditions for each category [34]. On the economic level, the usage of the treated water is related to the ability to consistently produce the required commercial quantities with the same conditions. It might pose a great risk for corporations since production in the oil and gas industry is variable [35]. In addition to that, adequate infrastructure and proximity to an economically viable market are essential for using the treated water outside oilfield usage.
Moreover, this economic aspect is dependent on the water quality criteria and their associated costs. The more stringent and higher these criteria and purity, the greater the costs associated with the operations. Finally, on the social level, different factors can affect the implementation of treated water in non-oilfield industries. The perception of the public and their concerns regarding the risks associated with using treated water in other industries can pose a huge obstacle to the application of such a project [36]. Additional concerns might also arise regarding the utilisation of a short-term water supply to meet the long-term water needs of communities; consequently, public acceptance is essential for the success of this type of project.
Membrane technologies are crucial in modern wastewater treatment, offering efficient solutions for purifying water in industrial and environmental contexts. Recent advancements in membrane materials and structures have enhanced their durability and reduced fouling, leading to longer-lasting and more effective performance [37].
Pore size is critical in water treatment, particularly in the petroleum industry, where membranes are classified as microfiltration (MF), ultrafiltration (UF), nanofiltration (NF), and reverse osmosis (RO). MF has the largest pore size, with progressively smaller pores in UF, NF, and RO. Consequently, the hydrodynamic resistance to liquid passage increases from MF to RO [38].
Some essential features of these membrane technologies are summarised below.
Established in the 1960s for biological and pharmaceutical applications, MF has since been widely used in wastewater treatment [39]. It operates under pressure, filtering out particles with diameters ranging from 0.1 to 0.2 μm, including nanoparticles and fine microparticles [40]. MF is effective as a pretreatment to improve the performance of subsequent processes. It can remove dispersed oil droplets and heavy metals but may require additional processes, such as ultrafiltration, to handle smaller droplets and particulates [41].
UF is highly effective for treating low-salinity, less toxic produced water. It retains solids and solutes with a molecular mass above 300 kDa while allowing water and smaller solutes to pass through. UF is particularly useful for removing toxic heavy metals and is the most commonly used filtration process for rejecting oil from produced water and oily wastewater [42]. For optimal performance, chemical pretreatment before UF is recommended to enhance treatment efficiency [43].
In general, UF membranes are mostly prone to fouling due to high permeation flux. However, the most efficient way of minimising fouling is through making the membrane surface more hydrophilic and diminishing roughness.
Nanofiltration (NF) is one of the pressure-driven membrane techniques having separation effectiveness between ultrafiltration and reverse osmosis. This type of membrane employs a sieving mechanism and utilises the surface charge of the support layer to reject charged ions, even those smaller than the membrane's pore size [44]. This technique is gaining attention in wastewater treatment due to its lower energy consumption compared to RO and higher rejection efficiency than UF [45]. NF can remove specific molecules regardless of wastewater composition, is easy to operate, and reduces the number of stages needed, thereby lowering energy consumption [46].
RO uses semipermeable membranes to remove dissolved solids, ions, organics, and bacteria from wastewater. When the pressure exceeds the osmotic pressure, water flows from the concentrated side to the diluted side. Modern RO membranes consist of a thin-film composite (TFC) layer on an asymmetric UF membrane support, which, while highly selective, is prone to fouling due to the high pressure required [47]. RO membranes excel in rejecting a wide range of contaminants, including nitrates, pesticides, sulfates, fluoride, and bacteria. However, the environmental impact of disposing of byproducts from RO desalination, such as brine, is a concern. This brine is often dumped into the ocean, though it has the potential for further treatment.
The membrane bioreactor (MBR) is one of the most rapidly advancing technologies in wastewater treatment. MBRs integrate two different processes, microfiltration and ultrafiltration, in an effortless unit with traditional biological purification of active silt [48]. The key component of an MBR is its membranes, which act as a barrier to bacteria. It is an intensively growing technology and has serious competitors to other techniques based on the quality of water cleaning [49]. Generally, MBRs are favoured for applications with limited space and a high-quality treated water requirement. However, they are prone to membrane fouling and channel clogging, which can decrease permeability.
Membrane materials perform a pivotal role in various applications, particularly in membrane technology for separation processes. The establishment of new membrane materials is a significant research drive for academia, industry, and laboratories due to the challenges that membranes face from fouling, low permeability, and high impurity permeation with respect to strict selectivity desires [50]. Many kinds of materials exist, as explained below.
The usage of polymers is increasing and found in approximately every material utilised on a regular basis. The importance of polymers has been paid attention to in plenty of applications in distinct areas of technology, science, and industry [51]. Polymers have made an important contribution to wastewater treatment and have distinctive benefits that permit choosing the proper material type to address a separation issue [52]. To date, a variety of polymeric membranes have been established based on several distinct components like cellulose acetate (CA), cellulose nitrate, polyethersulfone (PES), polysulfone (PS), polyvinylidene fluoride (PVDF), polypropylene (PP), and polyacrylonitrile (PAN) [53].
Polymer membrane fabrication is a difficult process that consists of many steps: drying process, material selection, casting or hollow fibre spinning, dope solution preparation, phase inversion process, and posttreatment. Different methods are employed in the manufacturing of membranes, which are related to the material type and the desired application. The most common methods are the sol-gel technique, tubular and flat sheet extrusion, micro and nanofiber fabrication, and interface reaction − mainly when dealing with composite or multilayered membranes [54].
Polymer membranes are classified as porous and nonporous membranes. Porous membranes are utilised for microfiltration (pores of 0.1 to 10 μm) and ultrafiltration (pores of 0.001 to 0.1 μm). The smaller the pore sizes, the higher the selectivity; that is why porous polymeric membranes have appeared to be the fundamental technology in the field of separation [55]. On the other hand, nonporous membranes are used for reverse osmosis, characterised by their dense film, pressure or concentration permeate diffusion, and very small pore size (approximately 0.0001 to 0.001 μm) [56].
Ceramic membranes are known for their robustness, resistance to harsh chemical environments, and suitability for high-temperature applications. They are inorganic membranes of ceramic materials obtained by mixing additives of inorganic raw materials after reaction moulding and calcination at high temperatures. The average pore size is between 1−10 μm, and the total porosity inside of the membrane exceeds 30% [57]. Their role of separation characterises them based on screening theory, distinct permeabilities, and important pressure differences. Compared to polymer membranes, ceramic membranes are mostly widespread due to their significant features with respect to their lifetime and cost. Polymers cannot resist high temperatures, strict chemical environments, or strict conditions [58].
The type of ceramic materials depends on the membrane function and performance, based on several physical and chemical properties such as porosity, pore size, hydrophilicity, chemical and thermal strength, and mechanical stability, besides cost-effectiveness. Five common ceramic material types are active in producing ceramic membranes for water and wastewater treatment: alumina, zirconia, titania, silica, and zeolite [59].
Ceramic membranes are mostly made up of metal oxides, produced at high-temperature sintering, and have a hydrophilic characteristic due to the hydroxyl (−OH) groups on the membrane surface. However, the hydroxyl group density of the membranes is diminished nowadays due to high-temperature calcination [60]. Many technical modifications have progressed on ceramic membranes to decrease membrane fouling; the most effective ones include dip-coating, blending/doping, grafting, chemical vapour deposition, atomic layer deposition, sol-gel, and hydrothermal synthesis [61]. They present excellent chemical and thermal stability in aggressive conditions, making them appropriate for applications involving corrosive substances at high temperatures and having long lifespans. Nevertheless, ceramics can be brittle, and this challenge could be confronted through attentive design and material selection.
Thin film composite membranes (TFC) serve as semipermeable membranes predominantly employed in water purification processes, particularly gaining prominence in Nanofiltration (NF). The interest of TFC in NF lies in their structure, featuring a thin selective layer with robust mechanical strength, enabling high flux even under extreme pressures [62]. These membranes manifest as films comprising two distinct layers. The first layer, known as the support layer, contributes significantly to the membrane's mechanical robustness. On the other hand, the second layer termed the active or selective layer, plays a pivotal role in providing the membrane with selectivity. This layer functions by rejecting undesirable impurities while permitting the passage of water [63]. A notable limitation of TFC membranes is their susceptibility to a compressive effect when subjected to pressure. Elevated pressure causes the polymer to undergo slight rearrangement into a tightly fitting structure, resulting in reduced porosity and compromising the efficiency of systems utilising this material.
Further types also exist, such as metal membranes, composite membranes, cellulose-based membranes, and many others. However, ongoing research aims to develop novel membrane materials with improved efficiency, selectivity, and durability for a wide range of applications.
Membrane modules are essential for membrane-based separation processes, supporting the membranes and ensuring efficient operation across various applications. They are designed to hold membrane materials, provide proper sealing, and facilitate fluid flow through the membrane surface. The choice of module design depends on factors like the feed solution characteristics, desired permeate quality, and the scale of the separation process. The modules are categorised into several types described below.
This module is commonly used in reverse osmosis pretreatment and microfiltration membranes [64]. It is composed of four main elements: housing, tube sheet(s), a bundle of hollow fibre membranes with an inner diameter of less than 1 mm, and end caps. The hollow fibres provide coherent separation, support the membrane, and enhance the density and volume efficiencies [65]. Compared to the other modules, this type has the lowest pressure drop, the highest hold-up volume, the highest packing density, the easiest cleaning process, and is relatively cost-competitive. Despite the advantages of this module, pretreatment is usually necessary due to poor fouling control.
Spiral wound modules, initially designed for reverse osmosis, consist of folded membrane envelopes separated by spacers. These components are spirally wound around a perforated central tube, which collects the permeated water [66]. Recently, spiral wound modules have been adapted to separate acid gases from natural gas, expanding their applications beyond reverse osmosis. Two major advantages of spiral wound membrane modules are their ability to handle high pressure and their increased resistance to fouling, which contributes to a longer lifespan. These modules are typically housed in cylindrical pressure vessels and can be configured in parallel or series arrangements [67].
On the other hand, tubular modules, primarily constructed from ceramics or polymers, are widely used in microfiltration, ultrafiltration, and nanofiltration. These modules are known for their excellent antifouling properties and are often employed in treating highly polluted wastewater or viscous oil/water mixtures [68].
The Plate and Frame Module is known as the simplest module among the others. It is made up of plates, supporters, membranes, and spacers, all of which are connected in series form. There are two types of this module: dead-end plate frame system and cross-flow plate frame system. The main difference between them is the flow path of the feed solution [69].
One major advantage of tubular modules is their simple separation of solids from water, along with easy cleaning and replacement of the membranes [70]. Additionally, unlike plate and frame filters, tubular modules lack feed spacers, which reduces fouling issues and allows them to handle higher solid concentrations effectively. One of the major advantages of this module is that the separation of solids from water is quite simple, and the membrane can be cleaned and replaced very effortlessly. Another major advantage is that the filters of the plate and frame do not consist of any feed spacers, which diminish the fouling problem and handle enough solid concentrations. However, Balster [71] identified several drawbacks of this type, including 1) low packing density, 2) large pressure drop, and 3) lower efficiency compared to other structures. Plate and frame modules utilise flat sheet membranes in their structures [72]. This sheet is created by dissolving a polymer, such as PVDF, PES, or PS, in a solvent mixture to form a standardised dope solution. The dope solution is then applied to a thin film using a supporting layer for casting [73]. Due to its easy replacement, this sheet membrane structure is widely used in laboratory settings. Additionally, ceramic flat sheet membrane modules made from Silicon Carbide (SiC) are utilised in water filtration and membrane bioreactors [74].
Innovations should focus on developing new materials, refining module configurations, and advancing manufacturing techniques to improve module design, performance, and durability, as well as reduce fouling. Table 2 presents a summarised comparison of the different membrane types in terms of material, module, pore size, and main advantages and limitations [75]-[77].
Properties and characteristics of various membrane types
Membrane technology | Micro-filtration (MF) | Ultra-filtration (UF) | Nanofiltration (NF) | Reverse Osmosis (RO) | Membrane bio-reactor (MBR) |
---|---|---|---|---|---|
Membrane material | Polymer, ceramic | Polymer, thin-film composite membrane | Thin-film composite membrane | Polymer, ceramic | |
Membrane configuration | Hollow fibre, spiral wound, plate and frame | Spiral wound | Tubular, spiral wound, plate and frame | Hollow fibre, tubular and flat sheet | |
Pore size | 50–104 nm | 5–100 nm | 1–10 nm | < 2 nm | 5–1000 nm |
Advantages | Low energy cost, No extra safety consideration, Significant removal impact, Accuracy in the filtration process |
Low energy consumption, High efficiency, High permeation flux, Removal of toxic heavy metals |
High oil and organic molecule removal, Low energy consumption, Higher rejection, Simple to operate. |
Oil removal above 99%, Easy to operate and maintain, Low energy consumption, Needs less space | Bioreactors are small, A high degree of purification |
Major limitation | Regular cleaning required | Membranes cannot tolerate feed temperatures over 45°C | High tendency of membrane fouling |
Ultrafiltration, capable of separating particles up to 10 μm, falls between the ranges of Microfiltration and Reverse Osmosis. This membrane type operates with low energy consumption, making it effective for the removal of macromolecules and suspended solids. Microfiltration, targeting particles up to 0.2 μm, serves as a suitable pretreatment for NF and RO membrane processes. Its efficiency is enhanced with the application of pretreatment processes, as demonstrated by a 90.2% removal effectiveness of organic additives in oily water [78]. Nanofiltration excels in removing ions, enabling operation at pressures lower than RO. It makes NF membrane processes recommended for heavily polluted waters to enhance proficiency. In contrast, Reverse Osmosis selectively permeates water molecules due to their tight pores, distinguishing it from other membrane processes [79].
Transitioning from theoretical approaches to real-world applications is crucial for understanding the role of membrane separation in produced water (PW) treatment. Real applications can be explored by examining published patents and their technical tests, as well as by considering the interest of commercial companies and ongoing pilot tests [80]. The following subsections provide a detailed discussion of various practical approaches for implementing membrane technologies in PW treatment.
Recent advancements in membrane technology have motivated a wave of patented innovations aimed at restructuring water management practices in the oil and gas industry. One such innovative patent, CN115353225A [81], introduces a novel approach to enhance the compatibility of flow-back and produced water for hydraulic fracking reinjection. Traditionally, poor compatibility between these water sources has led to significant permeability losses in reservoirs during reinjection. The proposed hybrid process combines a water quality stabiliser with a reverse osmosis system and a resin conversion system, facilitating improved mixing of diverse water systems, reducing scaling materials, and enhancing overall water management in oil and gas operations.
This patent is part of a wide trend where membranes are integrated with other technologies to elevate water management standards. For example, patent CN109851162B [82] influences membrane technologies alongside biochemical treatments to treat wastewater and produce industrial-grade crystallised salts. This integrated process not only reduces the trace required for wastewater treatment produced from oil and gas industries but also ensures that both treated water and manufactured salts comply with strict environmental regulations.
Additionally, patent CN112679020B [83] introduces a comprehensive hybrid treatment process for flow-back water, employing reverse osmosis, filtration, clarification, sediment removal, and electrodialysis. Specifically designed for water with high concentrations of salts and organic materials, this invention not only meets regulatory requirements for water reuse and discharge but also adds value to the process by producing high-quality industrial salts. The method, known for enhancing water treatment quality, reducing waste generation, and minimising chemical usage, holds potential for application in both flow-back water and produced water treatment processes, given their similar compositions.
These patented technologies represent significant steps in the quest for more efficient, sustainable, and cost-effective solutions for water management in the oil and gas industry. The integration of membrane technologies with other innovative processes displays a promising direction for advancing environmental oversight within the sector.
Manufacturing companies play a pivotal role in advancing membrane technology for the treatment of produced water in the oil and gas industry. With more industrial projects coming to life, several companies are focusing on manufacturing membranes to handle specifically produced water and its contaminants.
To illustrate some companies, Berghof Membranes specialises in tubular direct ultrafiltration membranes, which are recommended for the treatment of produced water following its separation from hydrocarbons in the 3-phase separator. After primary treatment using technologies such as coalescent plate interceptor (CPI), hydrocyclones, and flotations, Berghof's tubular ultrafiltration membranes effectively remove emulsified oil, solid particles, and bacteria. The treated water finds applications in Improved Oil Recovery (IOR) or can undergo further treatment for responsible disposal [84]. Noteworthy features include back-washable 5 mm membranes with a cross-flow process, offering fouling-resistant properties and high-quality permeate suitable for Reverse Osmosis feeds. Berghof's module design allows for reduced cleaning and maintenance frequencies, minimising system downtime and chemical costs [85].
Liqtech contributes to produced-water treatment with its Silicon Carbide Ultrafiltration membrane, designed for tertiary treatment to facilitate reinjection during IOR operations. This membrane efficiently removes oil in water emulsions and total suspended solids (TSS), extending the life of wells associated with reinjection at lower costs. Performance testing, using feeds from a hydraulic cyclone and an oil skimming tank, demonstrated a remarkable 95% efficiency with permeate streams of 1−5 ppm oil in water and 1−5 mg/L TSS. The silicon carbide material ensures durability, inertness, temperature resistance, and permeability [86].
ZwitterCo's Superfiltration membranes target the removal of high levels of fats, oils, and grease (FOG) from produced water streams. With a remarkable tolerance for Total Dissolved Solids content (>100,000 mg/L) and other chemicals, this membrane is recommended as a pre-desalination treatment step. Achieving up to 95% water recovery, ZwitterCo's membrane, produced from polymer materials, contributes to increased efficiency and decreased desalination costs. Its automated cleaning processes using generic chemicals further reduce maintenance and chemical requirements [87].
Hydranautics offers Integrated Membrane Solutions (IMS) tailored to the unique needs of the oil and gas industry. Their product line includes various ultrafiltration and membrane bioreactors, specialising in nanofiltration and reverse osmosis membranes mainly produced from polyamide and composite membranes. In an integrated approach, Hydranautics membranes are employed in both upstream and downstream sectors for water treatment, enabling reuse in processes such as Enhanced Oil Recovery (EOR), hydraulic fracturing, and boiler/cooling tower makeups. A secondary integrated approach, incorporating ultrafiltration, membrane bioreactors, and reverse osmosis, ensures compliance with customer specifications, allowing for water reuse outside the oil and gas industry [88].
In addition to more specialised companies, industrial projects handling produced water treatment using membranes are expanding. For instance, the China National Offshore Oil Corporation (CNOOC) implemented an innovative wastewater treatment approach by combining a Sequencing Batch Reactor (SBR) with a Ceramic Membrane Bioreactor (CMBR) for a plant designed to treat oil and gas field wastewater in Zhanjiang, China. The primary motivation behind establishing this plant was to protect the environment of the South China Sea. To ensure the successful application of the SBR+CMBR system, CNOOC conducted diverse lab-scale and pilot-scale experiments. Careful testing and experimentation were aimed at validating the efficacy and feasibility of the combined SBR and CMBR technologies. The total cost for the construction of this pioneering wastewater treatment facility amounted to approximately 671,800 USD, reflecting the commitment and resources allocated by CNOOC to address environmental concerns associated with oil and gas field wastewater treatment [89].
In addition, another project in Germany aims to introduce an innovative approach to treating produced water within the oil and gas industry, employing both flotation and ceramic micro-nano-membrane processes. The treatment plant is designed to effectively eliminate fine particles, organic matter, and ions from produced water, rendering it reusable through reinjection into wells to enhance oil production. Pilot plants were constructed, adhering to firm safety standards, and operated at industrial sites in Germany to ensure the practicality and viability of this method.
The implementation of ceramic membranes in the treatment process proved to be successful, particularly during the extraction of produced water from the exploration and production site in Barnstorf, Lower Saxony. The ceramic micro-nano-membrane technology demonstrated its efficacy in achieving the desired water quality standards. In addition to the technical aspects, the economic feasibility of this treatment method was inspected. The economic analysis highlighted that the treatment becomes an economically viable option when compared to alternatives that might be excessively expensive [90]. It marks the importance of considering economic factors alongside technological effectiveness in the evaluation of produced water treatment methods.
Challenges related to membrane fouling and scaling significantly impede the treatment of produced water [91]. For instance, particulate fouling occurs due to the accumulation of Total Suspended Solids on the membrane, leading to reduced flux and compromised process stability [92]. According to Ding et al. [93], addressing organic fouling is a delicate process, where an excess of major cleaning chemicals can potentially harm the membrane or intensify the problem. Organic fouling, originating from the deposition of oils and grease, poses a risk of permanent membrane damage [94]. On the other hand, scaling results from dissolved minerals surpassing the solubility limit in produced water [95]. This phenomenon reduces membrane permeability due to mineral deposits on the membrane surface and within its pores. Pretreatment of the flux entering membrane systems to remove dissolved and suspended solids from produced water helps mitigate scaling. Consequently, implementing both pretreatment and posttreatment steps becomes crucial to reduce such complications. Therefore, research endeavours should be directed towards enhancing membrane protection against these inherent risks.
Moreover, the characterisation of produced water poses an additional challenge for membrane treatments. The intricate composition of produced water adds complexity to the treatment process. For example, produced water containing surfactants can adversely impact the interaction between the water to be treated and the membrane. These surfactants may become adsorbed or accumulate on the membrane, and their micelles can obstruct the membrane pores [96]. Therefore, further research focused on characterising produced water is imperative to protect membranes from potential deterioration.
In fact, forthcoming research efforts should prioritise hybrid processes that integrate membranes with other technologies to enhance cost-effectiveness. This emerging trend is particularly notable in recent patents and projects globally. Hybrid processes not only allow for better economic factors but also allow many membrane types to reach their potential efficiencies [97]. Additionally, the adoption of renewable energy sources helps to reduce the facility's environmental footprint. Hence, it is imperative to conduct thorough investigations into suitable pretreatment, treatment, and posttreatment processes for hybridisation, aiming to attain the desired water quality with minimal energy costs and environmental impacts.
It is also important to emphasise that the upscaling of pilot plants and projects to industrial-scale facilities necessitates careful consideration. The volume of water provided for treatment must be carefully determined, not only in terms of plant capacity but also discharge, reinjection, or reuse targets. For instance, reinjection in oil or gas fields, depending on field properties, may pose a threat, potentially inducing seismic activity in the area [98]. Consequently, reinjection volumes cannot be infinitely increased, and a predetermined volume for reinjection must be established. In addition, thorough economic studies are imperative for the transition from laboratory scale to commercial facilities. While numerous studies have explored membrane and hybrid processes for produced water treatment on laboratory scales, a comprehensive upscaling plan for many successful studies and projects is yet to be developed [99]. This process requires meticulous studies and considerations before large-scale implementation.
As the oil and gas industry grapples with increasing volumes of produced water, effective water management becomes crucial. Reinjection stands out as a cost-effective means of reusing produced water within the industry, and additional treatments can enhance its quality for use in various sectors. Membrane technologies for produced water treatment are explored in this review, evaluating the advantages and disadvantages of each system. However, challenges like membrane fouling and scaling persist.
Membrane fouling, impacting performance through reduced flux and stability, requires sensitive cleaning processes to avoid damage. Scaling risks can be mitigated through pretreatment, emphasising the need for comprehensive steps to address these complications. Further research is imperative to safeguard membrane performance, addressing the complexity of produced water challenges.
Environmental considerations are vital, especially regarding byproduct disposal. Rejecting salts and toxic concentrates from water treatments poses risks to environmental well-being, emphasising the need for greener alternatives. Future research should focus on hybrid processes, combining membranes with other technologies, and utilising environmentally friendly energy sources. Finally, economic studies are pivotal for upscaling successful laboratory studies to commercial on-field plants, a critical step for large-scale implementation.
BTEX | Benzene, Toluene, Ethylbenzene, and Xylenes |
CA | Cellulose Acetate |
CMBR | Ceramic Membrane Bioreactor |
CNOOC | China National Offshore Oil Corporation |
CPI | Coalescent Plate Interceptor |
EOR | Enhanced Oil Recovery |
EPA | Environmental Protection Agency |
FOG | Fats, Oils, and Grease |
GWC | Gas-Water Contact |
IMS | Integrated Membrane Solutions |
IOR | Improved Oil Recovery |
MBR | Membrane Bioreactor |
MF | Microfiltration |
NF | Nanofiltration |
OSPAR | Oslo and Paris Convention |
OWC | Oil-Water Contact |
PA | Polyamide |
PAN | Polyacrylonitrile |
PES | Polyethersulfone |
PP | Polypropylene |
PS | Polysulfone |
PVDF | Polyvinylidene Fluoride |
PW | Produced Water |
RO | Reverse Osmosis |
SBR | Sequencing Batch Reactor |
TDS | Total Dissolved Solids |
TFC | Thin Film Composite |
TSS | Total Suspended Solids |
UF | Ultrafiltration |
- , Membrane technologies in wastewater treatment: A review, 2020
Low-impact Management of Produced Water: Assessing Phytodepuration with Halocnemun Strobilaceum and Suaeda fruticosa ,Journal of Sustainable Development of Energy, Water and Environment Systems , Vol. 12 (2),pp 1–11 , 2024, https://doi.org/https://doi.org/10.13044/j.sdewes.d12.0494
, Produced Water from Oil and Gas Exploration—Problems, Solutions and Opportunities ,J Water Resour Prot , Vol. 14 (02),pp 142–185 , 2022, https://doi.org/https://doi.org/10.4236/jwarp.2022.142009
, - , From waste to resource: Membrane technology for effective treatment and recovery of valuable elements from oilfield produced water, 2024
Oilfield-produced water characteristics and treatment technologies: a mini review ,IOP Conf Ser Mater Sci Eng , Vol. 1058 (1),pp 012063 , 2021, https://doi.org/https://doi.org/10.1088/1757-899x/1058/1/012063
, - , Recycling and re-usage of oilfield produced water – A review, Materials Today:, 2023
The influence of production chemicals on the quality of oilfield produced water ,Journal of Sustainable Development of Energy, Water and Environment Systems , Vol. 9 (4), 2021, https://doi.org/https://doi.org/10.13044/j.sdewes.d8.0319
, - , Produced water characteristics, treatment and reuse: A review, 2019
- , Advances in Produced Water Treatment Technologies: An In-Depth Exploration with an Emphasis on Membrane-Based Systems and Future Perspectives, 2023
Water Production Problem in Gas Reservoirs: Concepts, Challenges, and Practical Solutions ,Math Probl Eng , Vol. 2021 , 2021, https://doi.org/https://doi.org/10.1155/2021/9075560
, Effect of heterogeneity on the productivity of vertical, deviated and horizontal wells in water drive gas reservoirs ,J Nat Gas Sci Eng , Vol. 23 ,pp 481–491 , 2015, https://doi.org/https://doi.org/10.1016/j.jngse.2015.02.027
, - , Fundamentals of Reservoir Fluid Behavior, Reservoir Engineering Handbook, 2019
Conventional diverting techniques and novel fibr-assisted self-diverting system in carbonate reservoir acidising with successful case studies ,Petroleum Research , Vol. 6 (3),pp 247–256 , 2021, https://doi.org/https://doi.org/10.1016/j.ptlrs.2021.01.003
, The influence of hydraulic fractures on oil recovery by water flooding processes in tight oil reservoirs: An experimental and numerical approach ,J Pet Sci Eng , Vol. 185 , 2020, https://doi.org/https://doi.org/10.1016/j.petrol.2019.106572
, Estimation of fracture production and water breakthrough locations of multi-stage fractured horizontal wells combining pressure-transient analysis and electrical resistance tomography ,J Pet Sci Eng , Vol. 194 , 2020, https://doi.org/https://doi.org/10.1016/j.petrol.2020.107479
, The impact of connate water saturation and salinity on oil recovery and CO2 storage capacity during carbonated water injection in carbonate rock ,Chin J Chem Eng , Vol. 27 (7),pp 1699–1707 , 2019, https://doi.org/https://doi.org/10.1016/j.cjche.2018.09.008
, - , SPE-199498-MS Reuse of Produced Water in the Oil and Gas Industry, 2020
Optimal selection of an integrated produced water treatment system in the upstream of oil industry ,Process Safety and Environmental Protection , Vol. 117 ,pp 67–81 , 2018, https://doi.org/https://doi.org/10.1016/j.psep.2018.04.010
, - , Reuse of produced water from the onshore oil and gas industry, 2020
- , State of the art of produced water treatment, 2018
Enhancement of COD removal from oilfield produced wastewater by combination of advanced oxidation, adsorption and ultrafiltration ,Int J Environ Res Public Health , Vol. 16 (17), 2019, https://doi.org/https://doi.org/10.3390/ijerph16173223
, Oil and Gas Production Wastewater: Soil Contamination and Pollution Prevention ,Appl Environ Soil Sci , Vol. 2016 ,pp 1–24 , 2016, https://doi.org/https://doi.org/10.1155/2016/2707989
, Oilfield produced water treatment to clean water using integrated activated carbon-bentonite adsorbent and double stages membrane process ,Chemical Engineering Journal , Vol. 347 ,pp 462–471 , 2018, https://doi.org/https://doi.org/10.1016/j.cej.2018.04.136
, Recent advances on the treatment of oil fields produced water by adsorption and advanced oxidation processes ,Journal of Water Process Engineering , Vol. 49 ,pp 103034 , 2022, https://doi.org/https://doi.org/10.1016/j.jwpe.2022.103034
, - , Produced water: Oil and gas terminology glossary, Fact Sheet. Water Environment Federation, 2018
- , Fit-for-purpose treatment goals for produced waters in shale oil and gas fields, 2020
- , New advancements, challenges, and future needs on treatment of oilfield produced water: A state-of-the-art review, 2022
A risk-based approach to produced water management in offshore oil and gas operations ,Process Safety and Environmental Protection , Vol. 139 ,pp 341–361 , 2020, https://doi.org/https://doi.org/10.1016/j.psep.2020.04.021
, The effects of salt concentration on the rejection of pharmaceutically active compounds by nanofiltration membranes ,Journal of Sustainable Development of Energy, Water and Environment Systems , Vol. 9 (3), 2021, https://doi.org/https://doi.org/10.13044/j.sdewes.d8.0356
, - , Produced Water Treatment Technologies: An Overview, Chapter in “Solid–Liquid Separation Technologies”, 2022
Sustainable technologies for on-site domestic wastewater treatment: a review with technical approach ,Environ Dev Sustain , Vol. 24 (3),pp 3039–3090 , 2022, https://doi.org/https://doi.org/10.1007/s10668-021-01599-3
, - Produced Water Report, 2023, https://www.gwpc.org/wp-content/uploads/2023/06/2023-Produced-Water-Report-Update-FINAL-REPORT.pdf., Report
- Produced water discharges from offshore oil and gas installations 2009-2019, 2022, https://www.ospar.org/documents?v=48861.
- , Summary of Input on Oil and Gas Extraction Wastewater Management Practices Under the Clean Water Act, 2020
- , Successful Control of High Water Production with Thixotropic Conformance Technology in a Horizontal Well: Diagnosing the Water Production Mechanism., Paper presented at the SPE/ICoTA Well Intervention Conference and Exhibition, Texas, USA, 2020
- , An Effluent Stream Treatment and Analysis System to Counteract Water Availability & Usage Issues for Unconventional Oil & Gas Resources., SPE Argentina Exploration and Production of Unconventional Resources Symposium, Buenos Aires, Argentina, 2016
- , Membrane technology for water and wastewater management and application in Egypt, NIDOC (Nat.Inform.Document.Centre), 2017
- , Ultrafiltration Membrane Technology for Oily Wastewater Treatment, IOP Conference Series: Earth and Environmental Science, 2021
- , Introduction to membrane technology, Membrane Contactor Technology: Water Treatment, Food Processing, Gas Separation, and Carbon Capture, 2022
- , Membrane Separation Technology for Wastewater Treatment and its Study Progress and Development Trend
- , Use of membrane technology for oil field and refinery produced water treatment - A review, 2016
- , Oilfield-produced water treatment using conventional and membrane-based technologies for beneficial reuse: A critical review, 2022
An Environmental Performance Analysis of Upgraded and Integrated Treatment Techniques for Drinking Water Production through Reclamation ,Journal of Sustainable Development of Energy, Water and Environment Systems , Vol. 10 (2), 2022, https://doi.org/https://doi.org/10.13044/j.sdewes.d9.0393
, Industrial wastewater treatment by nanofiltration—a case study on the anodising industry ,Membranes (Basel) , Vol. 10 (5), 2020, https://doi.org/https://doi.org/10.3390/membranes10050085
, - , Wastewater treatment by nanofiltration membranes, IOP Conference Series: Earth and Environmental Science, Institute of Physics Publishing, 2018
Nanofiltration Treatment of Industrial Wastewater Doped with Organic Dye: A Study of Hydrodynamics and Specific Energy ,Processes , Vol. 10 (11), 2022, https://doi.org/https://doi.org/10.3390/pr10112277
, - , Forward Osmosis Membrane Technology for the Petroleum Industry Wastewater Treatment, Applied Water Science, 2021
Cost aspects of membrane bioreactors for wastewater treatment ,IOP Conf Ser Earth Environ Sci , Vol. 177 ,pp 012037 , 2018, https://doi.org/https://doi.org/10.1088/1755-1315/177/1/012037
, - , Membrane Bioreactors for Produced Water Treatment: A Mini-Review, 2022
A review of polymeric membranes and processes for potable water reuse ,Prog Polym Sci , Vol. 81 ,pp 209–237 , 2018, https://doi.org/https://doi.org/10.1016/j.progpolymsci.2018.01.004
, Review: Polymers, Surface-Modified Polymers, and Self Assembled Monolayers as Surface-Modifying Agents for Biomaterials ,Polymer - Plastics Technology and Engineering , Vol. 54 (13),pp 1358–1378 , 2015, https://doi.org/https://doi.org/10.1080/03602559.2015.1021488
, - , Nanostructured Polymer Membranes: Applications, State-of-the-Art, New Challenges and Opportunities, 2016
Polymeric Membranes for Oil-Water Separation: A Review ,Polymers (Basel) , Vol. 14 (5),pp 980 , 2022, https://doi.org/https://doi.org/10.3390/polym14050980
, Grand Challenge in Membrane Fabrication: Membrane Science and Technology ,Frontiers in Membrane Science and Technology , Vol. 1 , 2022, https://doi.org/https://doi.org/10.3389/frmst.2022.883913
, - , A review on porous polymeric membrane preparation. Part I: Production techniques with polysulfone and poly (vinylidene fluoride), 2019
- , Membrane materials for water purification: Design, development, and application, Royal Society of Chemistry, 2016
- , Application of Ceramic Membrane in Water and Wastewater Treatment, E3S Web of Conferences, 2018
- , Preparation of Ceramic Membranes and Their Application in Wastewater and Water Treatment, 2023
- , Ceramic-based membranes for water and wastewater treatment, 2019
- , State-of-the-art ceramic membranes for oily wastewater treatment: Modification and application, 2021
Preparation and characterisation of TiO2 and γ-Al2O3 composite membranes for the separation of oil-in-water emulsions ,RSC Adv , Vol. 6 (6),pp 4877–4888 , 2016, https://doi.org/https://doi.org/10.1039/C5RA23523E
, Development of Thin-Film Composite Membranes for Nanofiltration at Extreme pH ,ACS Appl Polym Mater , Vol. 3 (11),pp 5912–5919 , 2021, https://doi.org/https://doi.org/10.1021/acsapm.1c01172
, A Mini-Review on Thin-Film Composite Hollow Fiber Membranes for Forward Osmosis Applications ,Ecological Engineering & Environmental Technology , Vol. 24 (1),pp 287–301 , 2023, https://doi.org/https://doi.org/10.12912/27197050/154954
, membranes Recent Progress and Challenges in Hollow Fiber Membranes for Wastewater Treatment and Resource Recovery ,Membranes (Basel) , Vol. 11 ,pp 839 , 2021, https://doi.org/https://doi.org/10.3390/membranes
, - , Membrane Shapes and Modules, Science and Technology of Separation Membranes, 2017
Fabrication and scale-up of multi-leaf spiral-wound membrane modules for CO2 capture from flue gas ,J Memb Sci , Vol. 595 ,pp 117504 , 2020, https://doi.org/https://doi.org/10.1016/j.memsci.2019.117504
, Multicomponent spiral wound membrane separation model for co2 removal from natural gas ,Membranes (Basel) , Vol. 11 (9), 2021, https://doi.org/https://doi.org/10.3390/membranes11090654
, - , Tubular membranes and modules, Hollow Fiber Membranes, 2021
- , An Overview of Membrane Distillation Technology: One of the Perfect Fighters for Desalination, Engineered Science, 2022
A Review of Membrane Distillation Process: Before, During and After Testing ,International Journal of Engineering Technology and Sciences , Vol. 6 (1),pp 62–81 , 2019, https://doi.org/https://doi.org/10.15282/ijets.v6i1.1549
, - , Plate and Frame Membrane Module, Encyclopedia of Membranes, Berlin, Heidelberg: Springer Berlin Heidelberg, 2013
Comparative analysis of full-scale membrane distillation contactors - methods and modules ,J Memb Sci , Vol. 524 ,pp 758–771 , 2017, https://doi.org/https://doi.org/10.1016/j.memsci.2016.11.080
, - , Fundamentals of Membrane Processes, 2017
- , Membrane Fabrications, Membrane Technology for Water and Wastewater Treatment in Rural Regions, 2020
Membrane bioreactor for wastewater treatment: A review ,Case Studies in Chemical and Environmental Engineering , Vol. 4 ,pp 100109 , 2021, https://doi.org/https://doi.org/10.1016/j.cscee.2021.100109
, Direct and indirect effects of membrane pore size on fouling development in a submerged membrane bioreactor with a symmetric chlorinated poly (vinyl chloride) flat-sheet membrane ,J Environ Chem Eng , Vol. 10 (2),pp 107023 , 2022, https://doi.org/https://doi.org/10.1016/j.jece.2021.107023
, The Role of Membrane-Based Technologies in Environmental Treatment and Reuse of Produced Water ,Front Environ Sci , Vol. 9 , 2021, https://doi.org/https://doi.org/10.3389/fenvs.2021.629767
, - , Wastewater Treatment Using Membrane Technology, Wastewater and Water Quality, 2018
Biological Inspiration of Salt Exclusion Membranes in Mangroves toward Fouling-Resistant Reverse Osmosis Membranes ,The FASEB Journal , Vol. 31 ,pp S1 , 2017, https://doi.org/https://doi.org/10.1096/fasebj.31.1_supplement.949.2
, - , Commercial scale membrane-based produced water treatment plant, in Current Developments in Biotechnology and Bioengineering: Membrane Technology for Sustainable Water and Energy Management, 2023
- , Compatibility method of gas field fracturing flow-back fluid and oil field reinjection water, Pending patent CN115353225A, 2022
- , Oil and gas field salt-containing wastewater standard treatment process, Patent CN109851162B, 2022
- , Low-cost shale gas fracturing flowback fluid treatment system and treatment method, Patent CN112679020B, 2022
- Produced water treatment, https://www.berghofmembranes.com/oil-gas/produced-water-treatment.
- Robust tubular ultrafiltration, https://www.berghofmembranes.com/tubular-uf-membrane-modules.
- Produced water treatment reinjection case, https://liqtech.com/liquid-filtration-solutions/cases/produced-water-treatment-re-injectio.
- Produced water, https://zwitterco.com/solutions/produced-water.
- Brochure Oil and Gas, https://membranes.com/wp-content/uploads/2018/04/Brochure_Oil-and-Gas.pdf.
Treatment of High-Concentration Wastewater from an Oil and Gas Field via a Paired Sequencing Batch and Ceramic Membrane Reactor ,Int J Environ Res Public Health , Vol. 17 (6),pp 1953 , 2020, https://doi.org/https://doi.org/10.3390/ijerph17061953
, Sustainable industrial wastewater reuse using ceramic nanofiltration: results from two pilot projects in the oil and gas and the ceramics industries ,Journal of Water Reuse and Desalination , Vol. 10 (4),pp 462–474 , 2020, https://doi.org/https://doi.org/10.2166/wrd.2020.029
, - , Assessing the potential and limitations of membrane-based technologies for the treatment of oilfield produced water, 2023
Long-Term Performance of a Pilot Scale Combined Chemical Precipitation-Ultrafiltration Technique for Waste Brine Regeneration at Chevron Steam Flooding Plant ,Journal of Engineering and Technological Sciences , Vol. 52 (4),pp 501 , 2020, https://doi.org/https://doi.org/10.5614/j.eng.technol.sci.2020.52.4.4
, Fouling behavior of poly(vinylidene fluoride) (PVDF) ultrafiltration membrane by polyvinyl alcohol (PVA) and chemical cleaning method ,Chin J Chem Eng , Vol. 28 (12),pp 3018–3026 , 2020, https://doi.org/https://doi.org/10.1016/j.cjche.2020.05.032
, Removal of organic pollutants in shale gas fracturing flowback and produced water: A review ,Science of The Total Environment , Vol. 883 ,pp 163478 , 2023, https://doi.org/https://doi.org/10.1016/j.scitotenv.2023.163478
, Application of superomniphobic electrospun membrane for treatment of real produced water through membrane distillation ,Desalination , Vol. 528 ,pp 115602 , 2022, https://doi.org/https://doi.org/10.1016/j.desal.2022.115602
, Fouling of polyelectrolyte multilayer based nanofiltration membranes during produced water treatment: The role of surfactant size and chemistry ,J Colloid Interface Sci , Vol. 594 ,pp 9–19 , 2021, https://doi.org/https://doi.org/10.1016/j.jcis.2021.02.119
, The role of coagulation-flocculation in the pretreatment of reverse osmosis in power plant ,Journal of Sustainable Development of Energy, Water and Environment Systems , Vol. 8 (1),pp 118–131 , 2020, https://doi.org/https://doi.org/10.13044/j.sdewes.d7.0266
, Fracture Activation and Induced Seismicity During Long-Term Heat Production in Fractured Geothermal Reservoirs ,Rock Mech Rock Eng , Vol. 55 (8),pp 5235–5258 , 2022, https://doi.org/https://doi.org/10.1007/s00603-022-02882-z
, - , Machine-learning Assisted Induced Seismicity Characterization and Forecasting of the Ellenburger Formation in Northern Midland Basin, 2023